Projet de longue haleine, l’usine du futur vise des objectifs indispensables pour améliorer le fonctionnement des entreprises industrielles. Grandes comme petites, elles devront mieux exploiter les données fournies par les nouveaux outils logiciels (CFAO, gestion, etc.) ou ceux qu’elles possèdent déjà, profiter des solutions de communication tous azimuts, accélérer l’automatisation, améliorer l’intelligence de leurs moyens de fabrication… Vaste programme et un vrai parcours du combattant.
LE DÉFI connecter les équipements de production
LA SOLUTION une interface standardisée
Lancé en 2017 sous la houlette de la VDW (Association des constructeurs allemands de machines-outils) par 17 partenaires (Chiron, DMG Mori, Emag, Grob Werke, Heller, Liebherr Verzahntechnik, Trumpf, United Grinding, GF Machining Solutions, Pfiffner, Beckhoff, Bosch Rexroth, Fanuc, Heidenhain, ISW), le projet umati (universal machine tool interface) améliorera sensiblement la qualité et la productivité des ateliers. Brique importante du concept 4.0, cette initiative fait entrer la machine-outil dans le monde de la production intelligente. Le projet est passé en septembre dernier à un niveau supérieur : 70 constructeurs de 10 pays ont pour la première fois décidé de connecter leurs 110 machines et 28 services grâce à une interface universelle. Trois consortiums appartenant à des pays champions de la machineoutil ont également accepté d’y joindre leurs forces : ProdNet (Suisse), Edgecross (Japon) et NCLink (Chine).
Le projet umati est soutenu par les associations des constructeurs de machines-outils de Chine, Grande Bretagne, Italie, Pays-Bas, Autriche, Suisse, Espagne et Taiwan ainsi que par l’association européenne Cecimo. « Les machines-outils sont dotées d’une interface OPC UA (unified architecture) ainsi que d’un standard de communication industrielle dédié à l’IioT (internet industriel des objets) et au 4.0« , précise Alexander Broos, le responsable du projet umati. « Il permet de relier n’importe quelle machine-outil ou autre équipement sans frais et sans limitation géographique. Ces dernières communiquent en temps réel avec le système d’information de l’entreprise dotée d’une interface OPC UA et avec le cloud. » L’utilisateur peut ainsi identifier les différentes machines de son atelier, surveiller la production et chacune des pièces usinées, les temps de fabrication et le fonctionnement des machines, savoir quelles sont les opérations manuelles, détecter les aléas et les erreurs, réaliser des analyses statistiques de la production et construire des plannings, contrôler les outils de coupe… « Les versions futures d’umati s’enrichiront d’autres fonctions, comme les informations concernant les matériaux usinés, les contrôles du déroulement des opérations de fabrication et du système de gestion des données, le suivi de l’usure des machines et des équipements annexes pour assurer la maintenance prédictive, l’analyse du processus« , annonce Alexander Broos. Avec la possibilité à l’avenir, d’intégrer le système logistique de l’entreprise. D’autres initiatives s’ajoutent au projet umati, comme la « 5G alliance for connected industries and automation » (5G-ACIA) qui vise l’installation du réseau 5G dans l’atelier.
https://bit.ly/340rw6v
LE DÉFI contrôler l’usinage en temps réel
LA SOLUTION des capteurs installés sur le roulement de la broche qui détectent les surcharges et les risques de collision
Dans les opérations d’usinage, le roulement de la broche est un des composants qui doit faire face à des charges exceptionnelles car il doit transmettre les forces avec une précision maximale et à grande vitesse pendant des périodes assez longues. Le risque de surcharge et de collision n’est jamais totalement absent, ce qui provoque des arrêts intempestifs de la machine-outil. Le système de contrôle de la broche SpindleSense mis au point par Schaeffler réduit sensiblement les temps d’arrêts de machines-outils et améliore leur capacité productive. Des capteurs placés sur la bague des roulements de la broche d’usinage contrôlent le déplacement avec une précision de l’ordre du micromètre. Ce qui permet de détecter en moins de 2 millisecondes les aléas de production. Les capteurs SRS assurent des mesures radiales et axiales du déplacement du roulement de la broche dans cinq directions et sont disponibles avec un diamètre de 70, 80 ou 100 mm ainsi qu’une largeur de 16 mm. Le système transmet des signaux électriques à la commande numérique de la machine en cas de dépassement d’une certaine valeur établie pour chaque machine et broche. Les capteurs intègrent un logiciel maison. L’utilisateur dispose de deux options d’alerte :
- la variante C-A0 transmet des signaux d’alarme dès que les valeurs de charge et cinématiques ont été dépassées
- la variante C-A1 assure des mesures radiales et axiales des déplacements et les transmet via un bus CAN. Les constructeurs de machines-outils ou de broches peuvent utiliser ces mesures pour effectuer des analyses d’outils et améliorer l’utilisation de la broche. L’opérateur de la machine dispose quant à lui d’un outil qui lui indique avec précision le degré d’utilisation de la capacité de la broche dans chaque type d’usinage. Ce qui permet d’adapter la capacité de la
machine et prolonger ainsi son fonctionnement.
Les mesures transmises via le bus
CAN peuvent être utilisées également pour
la compensation du point zéro.
www.schaeffler.fr
LE DÉFI accélérer le transfert de données dans la fabrication
LA SOLUTION mise en place du réseau 5G
Lancée par la ZVEI (Association de fabricants électriques et électroniques allemands), l’Alliance 5G pour les industries connectées et l’automatisation (5G-ACIA) a comme principal objectif la meilleure applicabilité possible de la technologie 5G dans les usines. La 5G-ACIA identifie les besoins en spectre spécifiques des réseaux industriels 5G et explore de nouveaux modèles, par exemple pour l’exploitation de réseaux hôtes 5G dans la fabrication. Makino s’est allié avec Ericsson et Fraunhofer Institute for Production Technology (IPT) pour démontrer la faisabilité et les avantages de cette démarche. L’installation conçue par ces trois partenaires met en œuvre un robot qui récupère les outils dans un magasin, les transporte à une station de mesure et les charge dans la machine-outil grâce à un système de transport réalisé sur mesure. Les données sont transférées très vite entre la station de contrôle centrale et le robot via un réseau 5G. D’autres approches, comme « machine learning » (ML) et IA (intelligence artificielle), dopent également la production.
Le ML améliore le planning, l’ordonnancement et le contrôle des opérations, tandis que l’IA peut, via des commandes vocales, faciliter le contrôle de la machine-outil. Des développements à suivre…
www.5 g-acia.org
Date de publication : décembre 2019
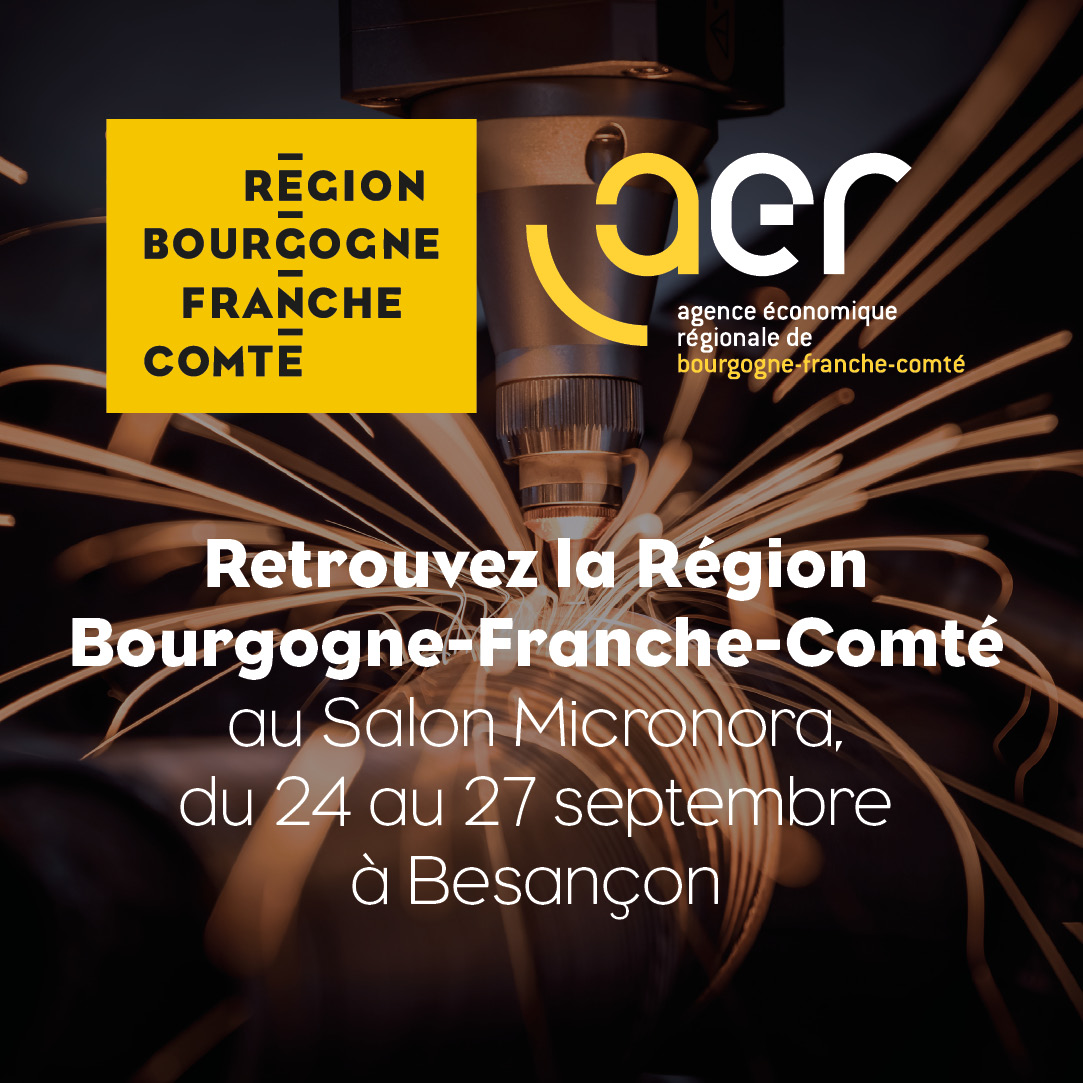
Sur le même sujet
mai 2025
Après une légère baisse d’activité l’année dernière, l’organisation professionnelle qui regroupe les fournisseurs de biens d’équipements, machines et solutions industrielles annonce une certaine reprise cette année. "Le BTP ainsi que [...]
mai 2025
Davy Pillet, CEO d’Ellistat Davy Pillet, CEO d’Ellistat : "Le principal frein à l’automatisation des machines-outils reste le temps de configuration d’une nouvelle pièce. Lorsqu’un atelier doit produire plus de [...]
mai 2025
Support de tourelle pour machines de tournage avec une tourelle, une broche principale et une commande numérique Siemens. Source : Open Mind La suite CAO/FAO hyperMILL d’Open Mind offre une grande [...]