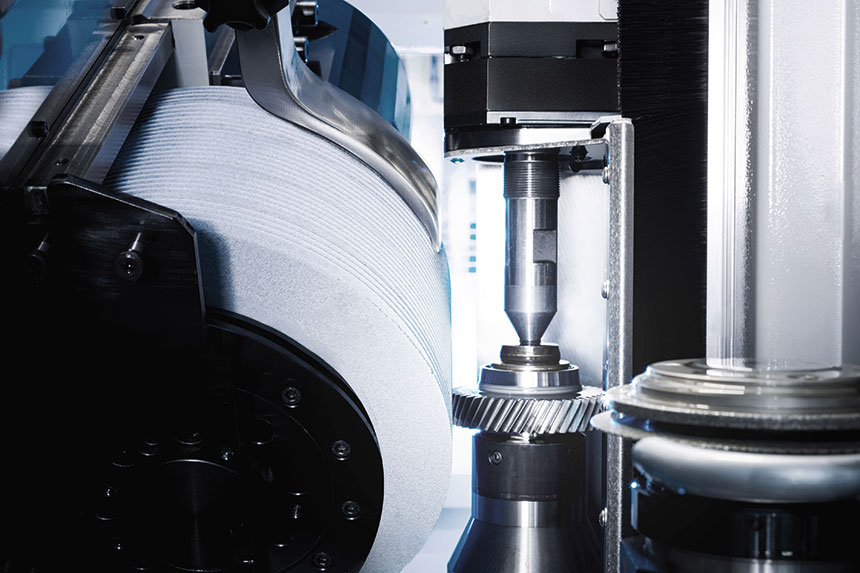
L’avènement inexorable de la voiture électrique bouleverse la fabrication automobile. Le moteur thermique, pièce maîtresse du véhicule classique cède la place à la batterie. Ce qui oblige les usines automobiles à se réinventer en adoptant de nouveaux moyens et méthodes de fabrication.
Processus complexe, la fabrication d’une voiture électrique marie la technologie avec l’ingénierie et le savoir-faire humain. Objectif : créer et produire des véhicules plus propres et plus efficaces. Tout commence au bureau d’études avec la mise en œuvre de nouveaux outils de conception. Prônée par des éditeurs comme Autodesk, Dassault Systèmes, PTC, TOPSOLID SAS ou Siemens Digital Industries Software, la conception générative améliore le bilan environnemental des voitures. « Avec les méthodes de conception traditionnelles, les utilisateurs réalisent généralement plusieurs concepts, les évaluent et les améliorent en fonction de leurs objectifs de conception », expliquent les spécialistes de Dassault Systèmes. « Le processus de conception générative commence toujours par l’explicitation des objectifs de conception. Ensuite, les algorithmes génèrent automatiquement des options de conception optimisées. On peut ainsi créer plusieurs versions, en identifiant les options nécessaires pour atteindre divers objectifs, par exemple, la réduction de poids. » La conception générative constitue donc un atout important pour améliorer les performances de la voiture électrique. En effet, dans un véhicule classique, c’est le moteur qui pèse le plus lourd tandis que dans un véhicule électrique, c’est la batterie. Car plus la batterie est grande, plus elle peut être chargée en électricité. Ainsi, la voiture roulera plus longtemps (ou plus vite).
Simuler avant de fabriquer
La conception générative permet aussi de choisir des matériaux appropriés. Grâce à elle, les constructeurs automobiles remplacent les composants classiques par des matériaux plus légers et recyclables, tels que l’aluminium, le magnésium ou les plastiques PLA. L’intégration des composants signifie également moins de pièces détachées. Exemple : General Motors qui, grâce à la conception générative et à la fabrication additive, a pu regrouper les huit éléments d’une console de siège en une seule pièce.
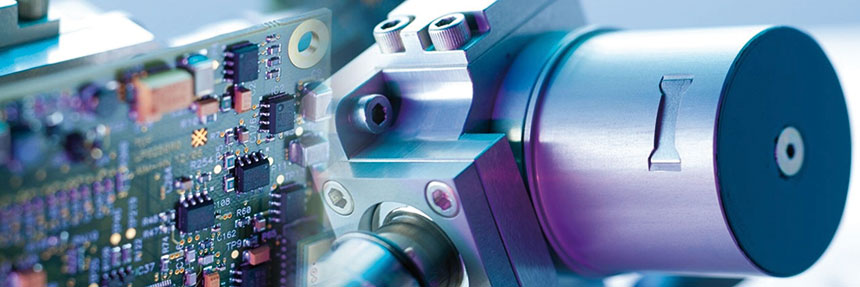
Comme Diehl Power Electronic qui propose des systèmes de contact cellulaires, des refroidisseurs PIN FIN, des anneaux de court-circuit en cuivre, des grilles découpées pour modules de puissance… Source : Diehl Power Electronic
Autre voie royale : la simulation qui s’invite aussi dans la conception de la voiture électrique. Le logiciel Simcenter E-Machine Design de Siemens Digital Industries Software aide les constructeurs de véhicules électriques (VE) et leur chaîne d’approvisionnement à prédire avec précision les performances des machines électriques, notamment les moteurs électriques à flux axial. « En regroupant les simulations électromagnétiques et thermiques, cet outil réduit le recours au prototypage physique et permet au secteur des VE d’innover plus vite », précise Jean-Claude Ercolanelli, vice-président principal responsable des solutions de simulation
et d’essai chez Siemens Digital Industries Software. « Il permet aux ingénieurs d’utiliser des modèles paramétriques et la modélisation analytique dès le début du développement, puis de continuer à travailler en 3D sur leur conception avec des simulations complètes d’analyse par éléments finis (FEA) lorsque des investigations plus complexes sont nécessaires, concernant, par exemple, les interactions thermiques avancées. » La fonctionnalité de capteur virtuel intelligent permet aux ingénieurs chargés des essais de simuler ce qui n’est pas mesurable. Elle intègre la simulation aux essais physiques en permettant de placer des capteurs virtuels dans les zones critiques.
Coté design, on peut repenser plus facilement l’aménagement des véhicules. La forme allongée, large et plate des batteries favorise les modèles à centre de gravité bas. Contrairement au moteur à combustion, le poids peut être réparti plus uniformément. Résultat : le châssis n’a pas besoin d’être aussi robuste et peut être plus léger.
Réduction des coûts de fabrication
Des procédés innovants, souvent alternatifs aux approches classiques de fabrication, se développent. Le procédé de formage à froid Conform Next d’Arnold Umformtechnik GmbH fait ses preuves dans la fabrication de composants coûteux et de haute qualité pour l’électromobilité. Plus lent, il permet d’intégrer les étapes de contrôle et d’assemblage. C’est une alternative économique aux pièces tournées ou fraisées coûteuses car les composants formés n’ont plus besoin d’être transférés vers une autre machine, voire une autre usine. Autre exemple d’innovation dans la fabrication : les nouveaux moyens de finition. Comme par exemple, les disques de freins en alliage dur (voir page 7 Un procédé sous la loupe). Dans la finition des engrenages, il s’agit également d’obtenir une qualité de surface de l’ordre du micromètre afin d’éviter que les composants de la denture ne génèrent des bruits de fonctionnement. Le moteur électrique étant silencieux, ces bruits deviendraient audibles. Les machines de rectification des dentures G 250 et G 160 du constructeur allemand Emag répondent à cet impératif, si important dans le domaine de l’e-mobilité. Ainsi, la G 160 n’a pas d’axe tangentiel, les axes Y et Z créant un axe tangentiel « virtuel » par un mouvement simultané. Plus grande, la machine G 250 assure la rectification par génération et de profil qui ont lieu sur la broche de rectification principale. Flexible, l’équipement peut passer en quelques minutes d’un procédé à l’autre. Dans le domaine de l’e-mobilité, cette approche est utilisée par exemple, pour la rectification des roues motrices des essieux. Emag propose également le procédé de rectification d’engrenages Sky Grind. Ce dernier permet de réduire sensiblement les coûts. La rectification finale de la roue dentée est ainsi réalisée à sec, ce qui évite l’installation de la filtration, du refroidisseur et d’autres dispositifs. Son secret : un système Dual-Tool avec deux broches d’outils différentes dans la machine (une pour la semi-finition par taillage, l’autre pour la finition par rectification).
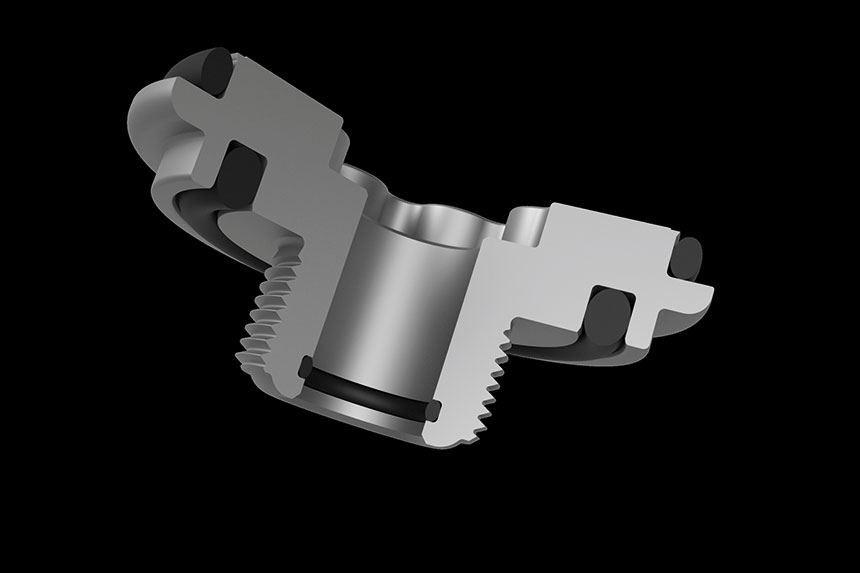
Les procédés de fabrication additive permettent à leur tour de réduire les coûts d’usinage, puisque le fraisage et le perçage sont éliminés voire réduits au minimum. Particulièrement bien adaptée à la production de batteries pour les véhicules électriques, elle offre une plus grande variété de géométries que les procédés classiques, ce qui réduit le poids des pièces. Autre avantage : l’intégration des pièces qui simplifie le montage ou le démontage pour les réparations et les mises à niveau des produits. La fabrication additive autorise la fabrication en flux tendu, ce qui élimine les stocks et l’entreposage de pièces détachées.
Des constructeurs comme Trumpf par exemple, se sont spécialisés dans cette technologie d’avant-garde. Le géant allemand dispose en outre, d’une gamme très large de solutions laser dédiées au soudage de jeux de barres, découpage, séchage et soudage des films de protection des batteries, etc. Sa technologie BrightLine Weld assure le soudage laser avec peu de projections des jeux de barres, des connecteurs souples ou des boîtiers de modules avec des lasers IR de haute puissance. Les lasers TruDisk à longueur d’onde verte préconisés sont adaptés aux matériaux hautement réfléchissants, comme le cuivre. Des profondeurs de pénétration de la soudure définies et constantes peuvent ainsi être réalisées et garantir des processus reproductibles.
Contrôle impitoyable de la qualité
L’amélioration de la fabrication de batteries est aussi dans la pointe de mire des ingénieurs de Siemens Digital Industries Software qui a lancé une collaboration avec Voltaiq. La plateforme Enterprise Battery Intelligence (EBI) de ce dernier, est utilisée par les équipementiers du secteur du transport, les sociétés mondiales d’électronique grand public, les fabricants de batteries et les développeurs de stockage d’énergie. Les solutions IoT (Internet des Objets) industrielles Insights Hub de Siemens, combinées à la suite complète de capacités de surveillance, de visualisation et d’analyse spécifiques aux batteries de Voltaiq, offrent une solution transparente de bout en bout pour gérer et optimiser la fabrication des cellules de batterie. Ce qui permettra de relever les principaux défis de la fabrication de batteries. Comme le contrôle qualité. En effet, il est difficile de s’assurer que chaque batterie répond aux normes les plus élevées en matière de performances et de sécurité. Les variations dans les conditions de fabrication peuvent entraîner des incohérences dans la qualité des batteries. Il est donc important de maintenir un contrôle qualité rigoureux tout au long de la production.
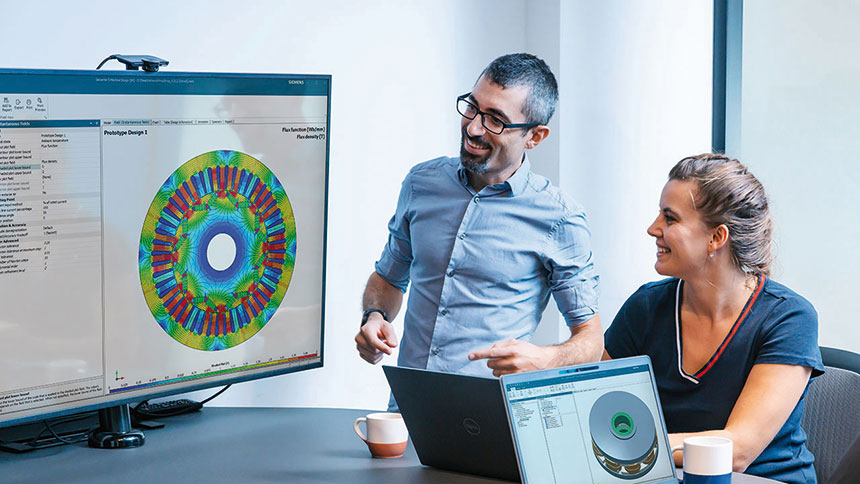
La productivité des usines est un autre défi. Cela implique une gestion efficace des installations automatisées à grande échelle avec des performances de machines constantes. La fabrication de batteries implique des processus chimiques complexes – une combinaison de processus par lots, de processus continus et de processus discrets – qui sont complexes à gérer. Cette complexité peut conduire à du gaspillage et à des inefficacités.
La société italienne Comau s’investit ainsi dans le développement de technologies d’entraînement électrique et élargit en permanence son portefeuille technologique pour répondre aux demandes en constante évolution des applications d’électromobilité. En plus de la conception, la fabrication et l’intégration de solutions d’automatisation flexibles, modulaires et évolutives, l’entreprise italienne est spécialisée dans les techniques d’assemblage de stator et de rotor, dans les systèmes d’assemblage d’entraînements électriques, de commandes électriques et dans les solutions d’usinage de boîtiers électriques. Comau gère aussi bien le prototypage et la fabrication de masse que le recyclage des batteries en fin de vie. La société s’est engagée à élaborer la stratégie de numérisation d’une plate-forme d’essai destinée aux systèmes de batteries de dernière génération dans le cadre d’un consortium multinational et pluridisciplinaire qui mène le projet Fastest. Cela devrait réduire le temps et les frais généraux de production des batteries d’au moins 20 % tout en diminuant le nombre d’expérimentations physiques. Une démarche basée sur la plate-forme d’IoT (Internet des Objets) In.Grid de Comau qui permettra d’analyser les données grâce au jumeau numérique. Ce qui raccourcira le délai de mise sur le marché pour les fabricants de batteries.
Les atouts de jumeaux numériques
Le projet Fastest est soutenu et promu par l’Union européenne dans le cadre du programme de recherche et d’innovation Horizon Europe. « À la différence des méthodologies d’essais actuelles, qui peuvent prendre des années et qui sont onéreuses, l’utilisation d’un jumeau numérique remplacera le premier déploiement physique par des modèles basés sur les données, accélérant ainsi le processus d’essai et de mise en œuvre », précise Stefania Ferrero, directrice marketing de Comau.
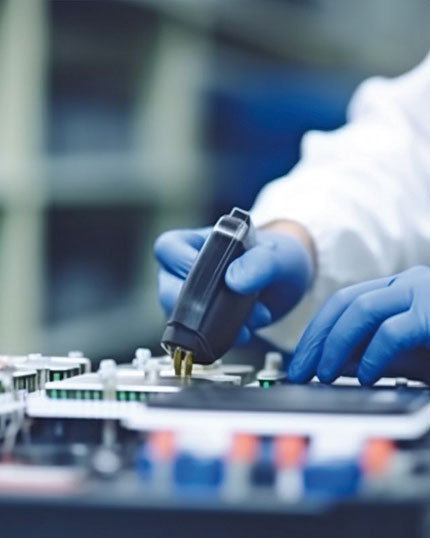
L’électronique de puissance (onduleurs, convertisseur de puissance DC/DC) joue également un rôle clé dans le pilotage du moteur, la gestion de l’énergie (dans le véhicule comme au freinage) et sa vitesse de charge. Ce qui explique le fait que dans un véhicule électrique, il y a plus de composants électroniques que dans un modèle thermique. De nouveaux composants à base de carbure de silicium et de nitrate de gallium vont aider à réduire la taille des composants tout en permettant une tension plus élevée. De nombreux spécialistes de la microélectronique fournissent ces solutions innovantes pour la voiture électrique. C’est le cas de Diehl Power Electronic qui propose des systèmes de contact cellulaires, des refroidisseurs PIN FIN, des anneaux de court-circuit en cuivre, des grilles découpées pour modules de puissance… Ses éléments de commutation innovants permettent d’atteindre une efficacité énergétique maximale dans les groupes motopropulseurs électriques et hybrides. Ils relient la fonction de connexion et de déconnexion à un limiteur de charge mécanique et assurent la limitation ou l’interruption du flux des forces dans le groupe motopropulseur. L’efficacité énergétique élevée et un couple moteur à bas régime dans chaque situation sont complétés par la possibilité de parvenir à un changement de vitesse à peine perceptible au niveau du bruit, des vibrations et de la dureté…
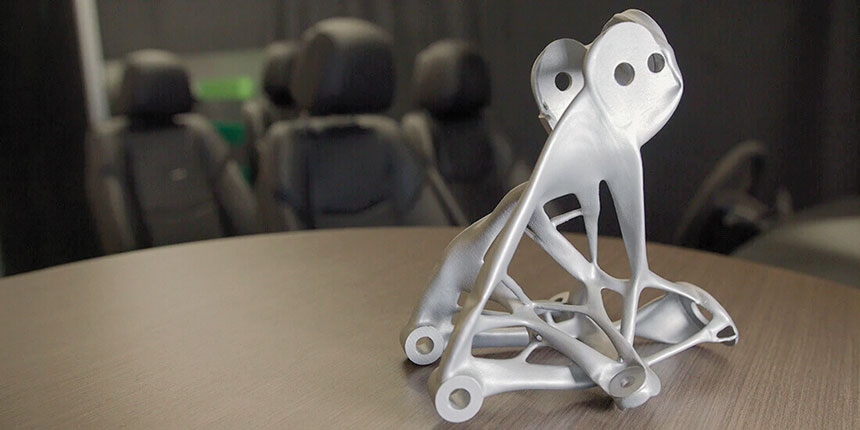
Vaste sujet, les solutions de fabrication de la voiture électrique ne peuvent pas être détaillées ici, mais les visiteurs du prochain salon Micronora qui aura lieu à Besançon (Doubs) du 24 au 27 septembre 2024, découvriront toutes ces technologies. Et bien d’autres innovations qui facilitent leur fabrication et recyclage…
Batteries : Bosch Rexroth automatise le recyclage
Construites selon les préceptes de l’Industrie 4.0, les usines qui fabriquent des voitures électriques font appel aux automatismes les plus avancés. Comme ceux de Bosch Rexroth conçus pour les opérations de démontage et de recyclage des batteries. Son procédé breveté est exploité dans la première usine entièrement automatisée d’Europe, la Battery Lifecycle Company. Mise en service à l’été 2023, cette dernière est née de l’alliance de Remondis TSR Recycling et de Rhenus Automotive. Jusqu’à 15 000 tonnes de matériaux de batterie par an seront recyclées dans cette unité de production ultramoderne. Grâce aux installations innovantes mises en œuvre, le processus qui prenait auparavant 24 heures dure désormais moins de 15 minutes. En recyclant les batteries, jusqu’à 95 % des éléments chimiques peuvent être réinjectés dans le processus de fabrication des batteries. Conçus sur mesure, les systèmes de convoyage transporteront chacun jusqu’à 150 kg à une vitesse de dix-huit mètres par minute. Destiné au transfert de charges lourdes, le TS5 imaginé par Bosch Rexroth est flexible. La diversité des modules offre une grande liberté pour le transfert ciblé des éléments de batteries. Par rapport aux systèmes dotés d’un entraînement traditionnel par chaîne, l’entraînement par arbre de transmission et les rouleaux du convoyeur du TS5 permettent un processus de production pratiquement sans entretien et avec une faible usure.
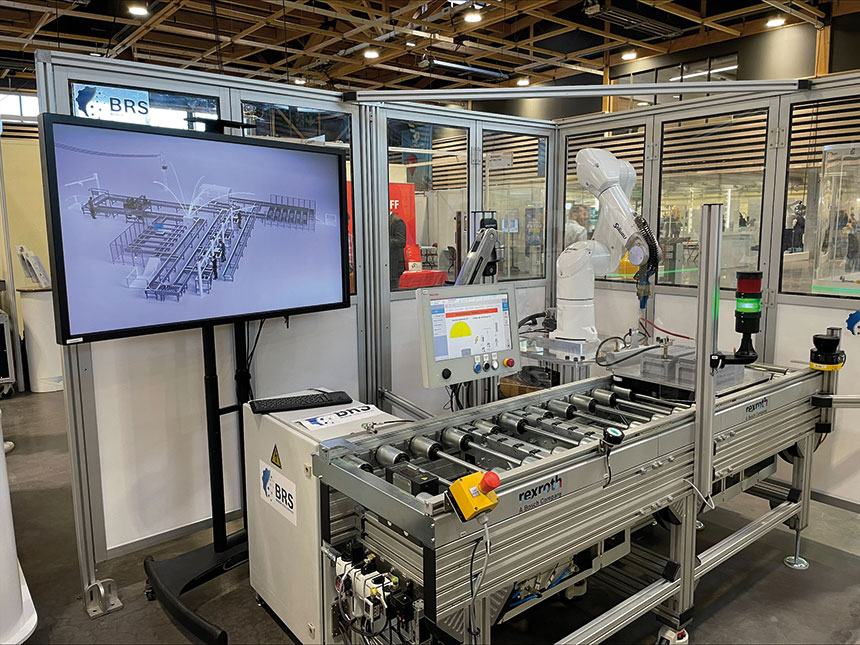
Ce système de transfert s’intègre dans l’architecture de contrôle ctrlX Automation, la boîte à outils d’automatisation pour la production de batteries de Bosch Rexroth qui supprime les frontières traditionnelles entre les systèmes de contrôle des machines, l’informatique et l’Internet des Objets. Inspirée du concept Smartphone, la ctrlX Automation peut être déployée dans une grande variété de secteurs, notamment automobile.
www.autodesk.fr
www.boschrexroth.com/fr/fr/
www.comau.com
www.diehl.com
www.emag.com
www.3ds.com/fr
www.ptc.com
www.topsolid.com
www.sw.siemens.com
www.trumpf.com/fr_FR/
Date de publication : mai 2024
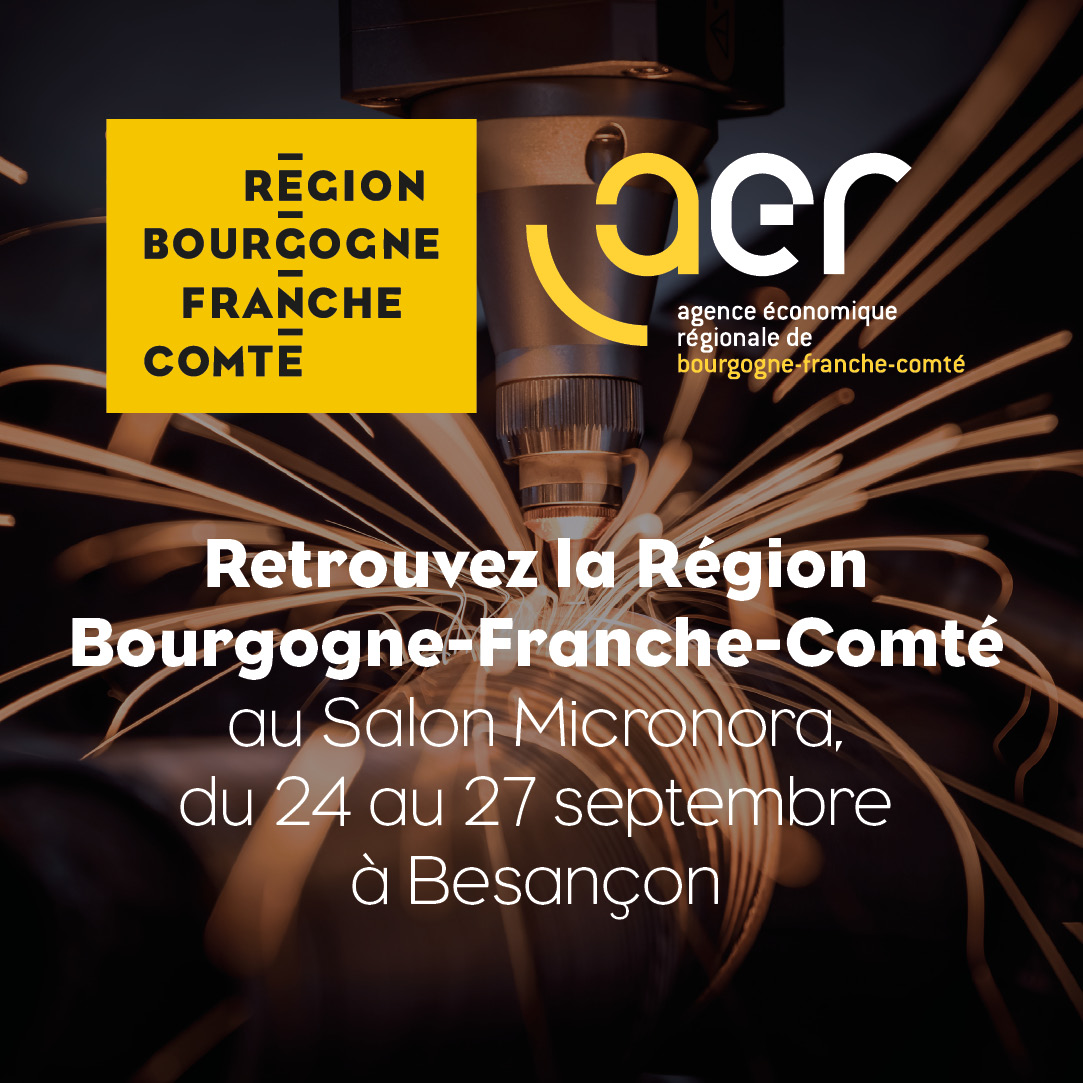
Sur le même sujet
mai 2025
ON EN PARLELes micro-news de l'industrieINNOVATIONLes prouesses technologiques du laserPRODUCTIONLe micro-moulage, source de profitsFOCUS ENTREPRISEVulkam construit sa première usineDOSSIERFabrication : des solutions qui dopent la productivitéR&D, PRODUITS ET SOUS-TRAITANCEL'ENTRETIEN DE MICRONORAFernando [...]
mai 2025
Disponible en 16 nouvelles références, les robots IRB 7710 et IRB 7720 d’ABB sont adaptés pour prendre en charge a applications dans l’industrie automobile allant de l’automatisation de la presse [...]
mai 2025
Ce système est conçu pour des travaux de soudage et de réparation précis et est adapté à une utilisation dans divers environnements de travail. Source : Alpha Laser Le AL-ROCK [...]