Miniaturisation extrême, performances hors normes, rationalisation de l’utilisation de matière première, réduction de l’impact environnemental, coûts mieux maîtrisés… Les fabricants de matériaux se surpassent pour répondre aux exigences de l’industrie microtechnique, avec de nouveaux alliages métalliques ou des solutions non métalliques originales.
Véritable mine d’or, Micronora, le salon international des microtechniques et de la précision, permet aux visiteurs de trouver la solution de production adaptée à leur projet. Une opportunité qui concerne également les matériaux, un ingrédient essentiel pour réussir le développement et la fabrication d’un produit, aussi bien dans l’industrie médicale ou aéronautique, automobile ou électronique, etc.
Miniaturisation extrême, réduction du poids et des coûts, meilleures performances mécaniques et respect des contraintes environnementales… Le développement de nouveaux matériaux correspond aux objectifs de nombreuses applications de pointe grâce à leurs propriétés avantageuses et à l’inventivité des chercheurs.
Un panorama qui se retrouvera dans le Zoom (cf. encadré page 17) du prochain salon Micronora qui aura lieu du 27 au 30 septembre 2022 à Besançon (Doubs). Les céramiques, les alliages amorphes, les composites à matrice métallique (CMM), les intermétalliques, les alliages bimétalliques, les alliages à haute entropie (HEA) et les alliages développés spécifiquement pour la fabrication additive métallique : autant de possibilités nouvelles pour réussir des projets industriels ambitieux.
Pour miniaturiser les éléments hautement sollicités
Connus depuis plusieurs dizaines d’années, les alliages métalliques amorphes (AMA ou verres métalliques) sont dotés d’une structure atomique désordonnée plutôt que cristalline. Dans l’industrie, 100 % des métaux sont en métal cristallin, mais cette structure atomique organisée est pleine de défauts. La structure atomique désorganisée des verres métalliques est totalement homogène, ce qui confère à ces matériaux des propriétés uniques : résistance mécanique, limite d’élasticité, comportement tribologique, dureté. Des atouts intéressants pour des applications à haute valeur ajoutée, comme l’horlogerie, le médical, l’aérospatial, etc, pour lesquelles la durabilité et la résistance mécanique sont cruciales. La société française Vulkam a réussi l’industrialisation de ces matériaux hors normes.
Baptisés Vulkalloys, ses alliages amorphes sont trois fois plus résistants que les alliages de titane. Ce qui améliore la miniaturisation des implants et la chirurgie mini-invasive. Ces alliages sont également amagnétiques et résistants au frottement, des qualités intéressantes pour la réalisation de mouvements horlogers plus performants. Les Vulkalloys sont 40 % plus légers que la fabrication en alliages d’aluminium, plus résistants à la corrosion que les aciers inox, inrayables et cinq fois plus performants que les aciers pour la transmission de puissance. « Ils peuvent être moulés comme le plastique, ce qui permet de limiter les pertes de matières et l’impact environnemental », précise Sébastien Gravier, co-fondateur avec Alexis Lenain, de Vulkam. Parmi les formulations proposées par la start-up française, le Vulkalloy Ni permet la réalisation de pièces micromécaniques (transmission de puissance, ressorts, vis, ou composants de micromoteurs). Le même alliage peut être utilisé dans l’industrie horlogère pour fabriquer des composants de mouvements (cliquets, roues, pignons, axes) tandis que le Vulkalloy Zr-Inox est adapté à la production de pièces d’habillage. Dans le domaine médical, les Vulkalloys Zr-Med et Nb-Med servent à la fabrication d’instruments dentaires et chirurgicaux, d’implants, de pinces, de visserie ou encore d’outils coupants… « Chaque formulation dépend des propriétés visées (résistance mécanique, au frottement, à l’usure ou à la rayure, tenue en fatigue, flexibilité, amagnétisme, résistance à la corrosion, biocompatibilité, etc.) », explique l’expert. « Ainsi, Vulkam a la capacité de coupler les propriétés exceptionnelles de ses matériaux à des procédés de fabrication spécifiques, pour produire en cadence des pièces à forte valeur ajoutée. »
Les instruments de microchirurgie ou dentaires en Vulkalloy répondent aux défis des fabricants de dispositifs médicaux : amélioration de l’ergonomie et des performances des instruments, grande précision du geste chirurgical, invasivité faible, grande durabilité des instruments.
De plus, ces alliages sont deux fois plus résistants que l’alliage médical de référence (TA6V), ce qui permet la réalisation de pièces jusqu’à deux fois plus petites. Les Vulkalloy Nb-Med sont, quant à eux, des alliages hautement résistants, adaptés à la production de composants de dispositifs médicaux fortement sollicités. Outre leurs propriétés mécaniques, ils se distinguent notamment par des propriétés en frottement exceptionnelles, une excellente résistance à la corrosion en milieu physiologique ainsi qu’une tenue en fatigue inégalable. La technologie plateforme développée par Vulkam constitue son cœur de savoir-faire. Elle est associée à des procédés complémentaires et spécifiques, déployés et optimisés par gamme de produits.
Des performances mécaniques hors normes
Associant une base métallique (aluminium) à un renfort de céramique (5 % à 20 % environ), les composites à matrice métalliques (CMM) se présentent soit sous forme de fibres courtes ou longues, soit sous forme de particules de petites (20-50 µm) ou de plus grosses tailles (millimétriques). La composition hybride des CMM allie les avantages de la structure métallique (tenue au choc, facilité de mise en forme…) avec ceux de la céramique (tenue à l’usure). Certaines imprimantes 3D sont capables de mélanger des particules de métal et de céramique (par laser cladding), ce qui pourrait accélérer le développement des CMM.
Autres matériaux intéressants, les alliages intermétalliques qui sont des composés métalliques. Ils se distinguent des alliages classiques par le caractère ordonné de leurs atomes dans la maille cristalline et leur caractère défini. Par exemple, un alliage FeAl est un alliage ordonné de fer et d’aluminium. Les atouts principaux de ces matériaux (résistance mécanique à haute température proche de celle des céramiques, aptitude à l’écrouissage propre aux métaux, haut point de fusion, faible diffusibilité, légèreté) expliquent l’intérêt de certaines industries. Les constructeurs aéronautiques cherchent ainsi des matériaux légers, mais capables de supporter des températures de fonctionnement toujours plus hautes. Réduction de masse, baisse de consommation de carburant, diminution des coûts de maintenance et des nuisances environnementales justifient le choix d’un matériau comme le TiAl qui est devenu l’alliage intermétallique le plus connu. D’autres familles d’intermétalliques (Fe3Al, FeNi…) sont toujours en développement.
« La mise en œuvre des alliages intermétalliques reste encore très délicate », expliquent cependant les spécialistes de Drimex, une entreprise spécialisée dans la sous-traitance industrielle.
« Cette approche reste confidentielle car elle nécessite des procédés industriels coûteux et ne peut pas encore s’étendre au-delà de certains secteurs hauts de gamme.Mais les intermétalliques subissent aussi d’autres freins à leur industrialisation : leurs fragilité (induisant une ténacité et une ductilité faibles), usinabilité difficile voire impossible et des mauvaises propriétés mécaniques à froid. Néanmoins, avec une production plus abordable, ils représenteront des concurrents sérieux à certains aciers et superalliages. »
Réduction des coûts et résistance à haute température
Assemblages de deux alliages, les bimétalliques apportent des économies de fabrication sensibles. Ils permettent ainsi d’utiliser un alliage noble (et donc souvent coûteux) là où il est réellement nécessaire et utile pour la fonction de la pièce (en zone de corrosion ou pour réaliser un renfort mécanique) et de mettre un alliage plus traditionnel dans le reste de la pièce. Différentes technologies permettent de réaliser des assemblages bimétalliques : insertion à la coulée, fabrication additive par laser cladding, soudage par friction malaxage (FSW) qui permet de souder des matériaux de composition hétérogènes, infiltration d’une structure lattice (en acier par exemple) issue de fonderie ou de fabrication additive par un alliage à plus bas point de fusion (aluminium par exemple). Le fabricant suisse Kugler Bimetal produit par exemple, des pièces mécaniques en acier qui ont une ou plusieurs faces recouvertes d’une fine couche de Tokat, un alliage anti-friction sans plomb. L’entreprise combine la fabrication additive par dépôt d’énergie dirigée (DED) avec l’usinage et le moulage. Cette solution offre la résistance à l’usure, la durabilité et la facilité de maintenance, des exigences essentielles dans des applications telles que l’éolien offshore, les pompes hydrauliques à haute performances, les boîtes de vitesses…
Résistants à hautes températures, les alliages à haute entropie ou HEA (High Entropy Alloy) ont été découverts en 2004. Elles contiennent au moins cinq éléments majeurs à égalité de composition et des éléments mineurs en plus faible quantité. Les applications visées sont la tenue à haute température ou en atmosphère ou milieu très agressif (aéronautique, énergie, nucléaire…). Dans l’industrie du nucléaire, ces alliages sont envisagés pour toutes les générations de réacteurs. Dans les réacteurs à eau pressurisée de génération deux actuels, ils remplaceraient certains éléments internes du circuit primaire en acier inoxydable austénitique (316) ou en Inconel 718, superalliage base nickel durci par précipitation de phases intermétalliques. Dans les futurs réacteurs à fission de génération 4, ils sont envisagés pour l’échangeur de chaleur des réacteurs à sel fondu de type MSR (Molten Salt Reactor). Et pour les futurs réacteurs à fusion, ils seraient utilisés en substitution aux alliages ferrito/martensitiques. « Les alliages à haute entropie offrent des propriétés mécaniques plus intéressantes que les alliages communs. Surtout pour les applications à hautes températures même au-delà de 600°C, température à laquelle un alliage commun perd significativement ses propriétés mécaniques », expliquent les spécialistes de Mécastyle, un bureau d’études qui maîtrise ces matériaux nouveaux. « La résistance à l’oxydation à des températures élevées sera améliorée si on utilise des composés adaptés comme l’aluminium, le chrome ou le silicium. L’alliage pourra alors être utilisé comme revêtement réfractaire (fonderie, moule d’injection plastique, outil de forgeage) ».
Des matériaux nouveaux pour la fabrication additive
La fabrication additive métallique se développe très fortement pour certains domaines industriels et applications. Pendant plusieurs années l’effort de développement a été mis principalement sur le développement des machines et les matériaux utilisés n’étaient pas optimisés pour ce nouveau procédé d’impression 3D (très forte vitesse de solidification, grains très fins…). Aujourd’hui, apparaissent de nouveaux alliages spécifiquement développés pour la fabrication additive. Exemple : la poudre de superalliage à base de nickel Amperprint 0233 Haynes 282. Ce matériau commercialisé par la société Haynes dispose d’une résistance au fluage élevée ainsi que de bonnes qualités de stabilité thermique et de soudabilité.
Plus facile à fabriquer, il est adapté aux applications structurelles à haute température telles que la production d’énergie, les turbines à gaz et les lanceurs spatiaux pour construire des pièces telles que des échangeurs de chaleur, des chambres de combustion, des buses, chemises de combustion, moteurs de fusée et roues à aubes enveloppées.
Heraueus AMLOY a mis au point un procédé qui permet aux machines de fabrication additive Trumpf de réaliser l’impression 3D des alliages amorphes. Ce qui simplifie sensiblement la production des pièces complexes.
Certaines entreprises spécialisées dans la fabrication additive, comme 3DCeram ou CeramTec, proposent de nouvelles solutions céramiques. « Les qualités de la céramique technique sont connues : grande résistance mécanique, stabilité dimensionnelle élevée, faible densité, très grande résistance à l’abrasion et à la corrosion, stabilité chimique exceptionnelle… », expliquent les spécialistes de 3DCeram. Des performances recherchées dans des industries comme le biomédical, l’aérospatial, le luxe… Utilisés par CeramTec pour différentes applications, les cermets sont constitués de matériaux céramiques à matrice métallique. Ce qui leur confère une très grande dureté et la résistance à l’usure. Des propriétés adaptées aux applications d’usinage qui nécessitent une haute qualité de surface, la stabilité dimensionnelle et des tolérances serrées. À savoir, les opérations de finition fine, la finition et l’ébauche de l’acier, du métal fritté et de la fonte ductile.
Spécialisée dans la métallurgie des poudres, la société Sintermat propose un procédé original : le frittage Flash ou frittage SPS (Spark Plasma Sintering). Les poudres sont agglomérées sous l’effet simultané d’une forte impulsion électrique et d’une charge uniaxiale (de l’ordre de 200 mégapascals). Ce qui permet d’obtenir sans usinage, des pièces complexes de grande résistance et à haute densité telles que des dents, cannelures, profils, etc. La densification de poudres et matériaux peut atteindre des vitesses généralement 10 à 100 fois plus élevées que celles des techniques de frittage traditionnelles. Le procédé assure la synthèse de matériaux massifs, innovants, originaux, à microstructures contrôlées, et ce, pour des coûts modérés. C’est l’une des seules technologies capable de produire des matériaux avec des microstructures sans grossissement des grains et avec un taux de densification voisin de 100%.
www.vulkam.com
www.trumpf.com
www.irepa-laser.com
www.lasercheval.fr
www.realmeca.com
www.heraeus.com
www.femto-st.fr
www.sinter-mat.com
www.3dceram.com
www.ceramtec.fr
www.haynesintl.com
www.bimetal.ch
www.mecastyle.com
www.sous-traiter.fr
www.bbfil.fr
www.cristal-innov.com
www.nanoe.com
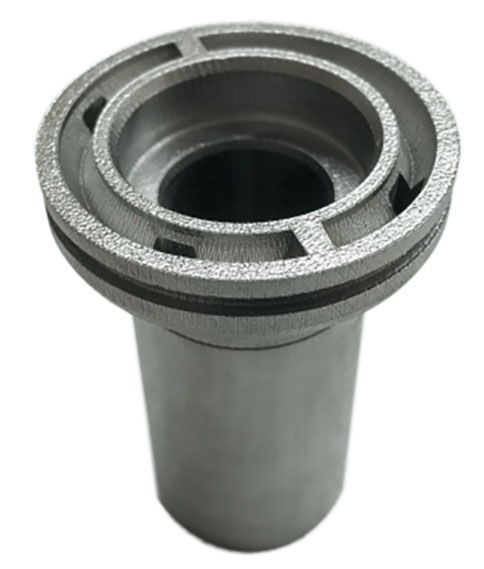
Zoom 2022 : Les nouveaux matériaux et nouveaux process dans les microtechniques
L’animation Zoom de Micronora 2022 présentera aux visiteurs plusieurs nouveaux matériaux et processus industriels. Les visiteurs découvriront ainsi des matériaux originaux et des pièces hors normes fabriquées par des sociétés comme Vulkam, Sintermat, IMI/Laser Cheval, BBfil, Cristal Innov, etc. Des sociétés comme Realmeca, Nanoe ou Irepa Laser présenteront des procédés de fabrication innovants, comme l’usinage par ultrasons, l’impression 3D de céramiques, d’aimants, d’alliages amorphes ou la recharge métallique. Quant à l’institut Femto-st, il dévoilera ses travaux de recherche pour développer les technologies d’usinage et de texturisation des carbures et des céramiques par l’intermédiaire des procédés avancés comme l’usinage par micro-usinage à l’outil coupant (micro-fraisage) et la texturation de surface par usinage laser. Femto-st dispose, grâce à sa plateforme MIFHySTO, d’une expertise dans le domaine des procédés de microfabrication mécanique et en particulier sur le micro-usinage (micro-fraisage, décolletage, µEDM…).
Un rendez-vous à ne pas manquer…
Sur le même sujet
mai 2025
Ce système robotisé réalise l’usinage de pièces complexes avec un coût réduit de 30 %. Une alternative particulièrement compétitive pour les nouveaux marchés en expansion. Source : SAB Robotique Ce système d’usinage [...]
mai 2025
Ce système est conçu pour des travaux de soudage et de réparation précis et est adapté à une utilisation dans divers environnements de travail. Source : Alpha Laser Le AL-ROCK [...]
mai 2025
La société MicroMécanique répond aux problématiques des environnements de production sous très fortes contraintes mécaniques et propose son savoir-faire dans le domaine de la réalisation d’outillages en carbure de tungstène. [...]